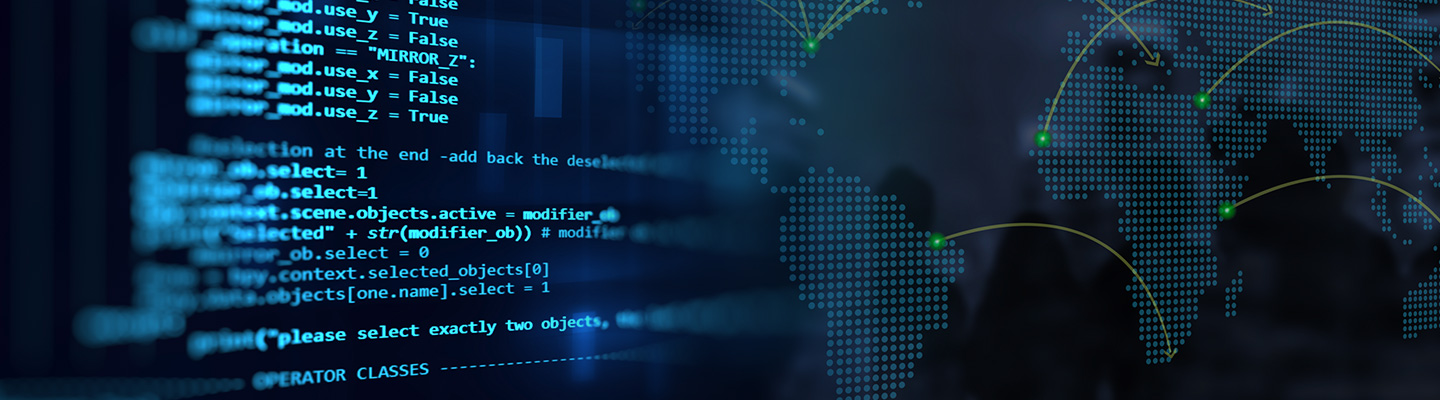
We develop MES solutions for the management, control and supervision of production, not only in the AUTOMOTIVE field.
MaTrace is the platform, produced by MATEC over the years, for the development of production management and control systems. Itconsists of a set of software modules, in constant evolution to respond to new market needs.
Since its origins, the "Factory IT" BU has developed software solutions in the industrial field for the collection of process data and the subsequent analysis, planning and production management.
Drawing on the MaTrace library, specific solutions are created, based on the Customer's requests (with obvious savings from an economic point of view) called CAP (Production Progress Control) and MTS (Matec Traceability Systems), our declination of MES (Manufacturing Execution System).
Production control and monitoring
At the second level of the so-called "Pyramid of automation" are positioned the DCS (Distributed control system), oriented to the process, and SCADA (Supervisory Control And Data Acquisition), oriented to the collection of data.
It is a constantly evolving technology, hand in hand with the progress of electronics, information technology and telecommunications networks, which allows the creation, operation and management of supervision, control and remote control systems.
CAP is the Matec solution which in this area allows:
- The optimization of the data collection process
- The centralization of information
- The representation of a SYNOPTIC on the state of the plant
- Monitoring of production progress through graphical interfaces and reports
- Alarm management
- Visualization on ANDON
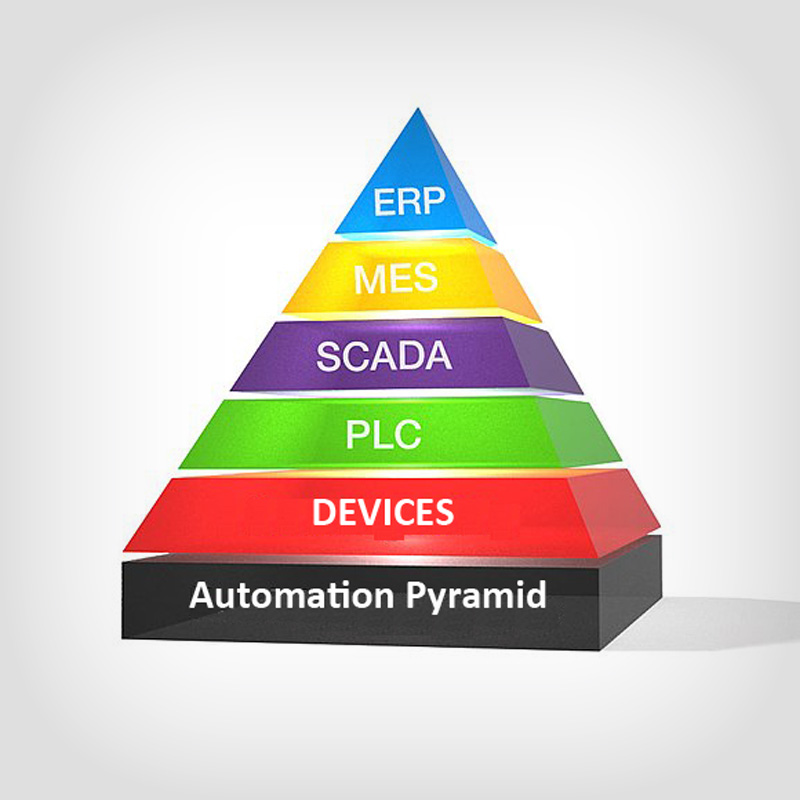
Product and process traceability
Traceability therefore consists in the ability to control all processes, from the procurement of raw materials to production, to shipping, up to the end user, logging all the data relating to the components, processes, movements of products and goods in general.
MTS systems are Matec solutions, tailored to the needs of each individual customer, which are placed at the intermediate level between FIELD and ERPwith the role of MES, i.e. a software system that is applied to manage the production process of a company, through direct connections to the machine(PLC/Scada) or manual declarations of the operators who are working. This information is provided in real time to the offices which thus have a complete view of thprogress of the orders, the physical state of the resources and the materials used. Furthermore, they can transmit the data to the management system already present ithe company (ERP)

Quality
In the context of a quality system, managed according to the ISO 9001 standard, the identification and traceability of the product are a requirement, as essential tools for quality management as they allow the product to be followed through all stages of production and, in case of non-compliance, to trace the causes and take corrective actions.
Using the tools that MTS makes available, the quality manager will be able to promptly detect the weak points of the production processes, plan corrective actions and finally monitor the continuous improvement of the processes by reducing their variability.
The application can provide the main "SPC" indicators such as sigma (estimated and real), cp, cpk, pp, ppk, cm, cpm, X/R charts and histograms with Gaussian
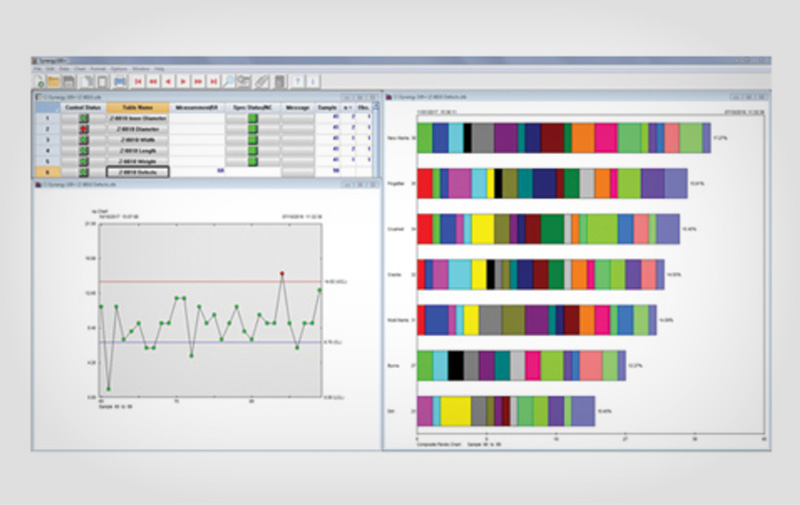
Industry 4.0
Our MES solutions have evolved from an Industry 4.0 perspective: one of the fundamental characteristics of Industry 4.0 systems, which is also explicitly required to access the tax credit (law n. 232 of 11/12/2016), is Automated integration with the factory logistics system, with the supply network and/or with other machines in the production cycle.
From this point of view, the 4.0 approach to the structure of the automation pyramid is based on the integration and interconnection between the MES and the field levelcomponents (PLC and SCADA systems). An integration between the two levels allows both real-time control of the production departments and, for example, the updating ofprogress declarations.
We have therefore made our platform integrable with the so-called "Systems for quality and sustainability assurance and devices for man-machine interaction":
- Machines capable of recognizing pieces (for example active systems such as RFID, passive systems such as QR codes, Visors and vision systems and mechatronics)
- Intelligent and connected systems for marking and traceability of production batches and/or single products
- Tools and devices for the labelling, identification or automatic marking of products (there are an example of systems capable of printing and applying the label onproducts automatically, without operator intervention)
- Connection systems between code and serial number of the product itself, in order to allow constant monitoring of product performance over time, allowing the recallof defective or harmful products
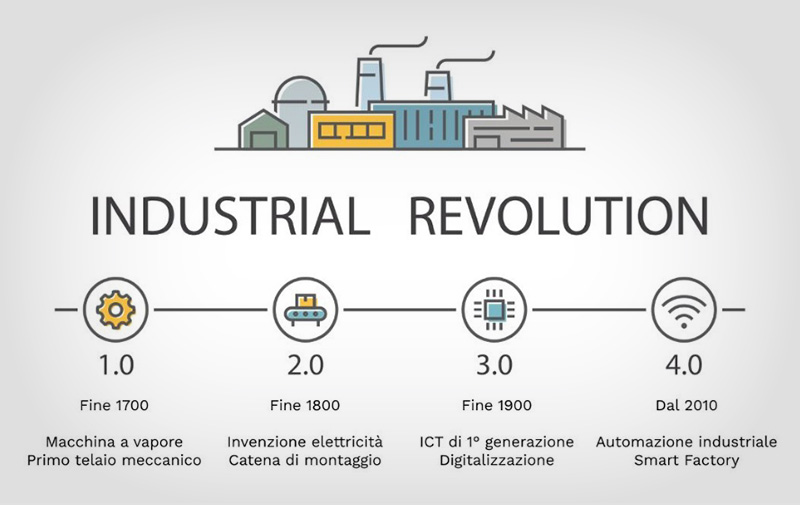
Industrial Internet of Things
An IIoT Platform (Industrial Internet of Things), in addition to the hardware level of the smart actuators, consists of a first level of signal processing (the IoT Gateway), with the task of lightening the processing of all the signals coming from the plant which would otherwise be up to the upper level.
This decentralized computing approach is called Edge Computing. The data sent is then processed for security management (generation of alerts and alarms), modeling and archiving, and made accessible to applications for real-time display and analysis.
The data provided by the IoT Platform to the MES also allow the implementation of integrated algorithms for the management of maintenance, also predictive, for the reduction of plant downtimes and a consequent and immediate increase in productivity.
